“Just in Time” and “Just in Case”: Two Well-Known Formulas that Seem to Differ by Just One Word but Conceal Much More. Today, let’s delve into a better understanding of what they mean in this article.
Warehouse: A Crucial Point for Production
Production has various needs and critical points, including the speed and efficiency of the production chain, training of operators, and reliability of machines.
The crucial point without which competing in the market is impossible is the warehouse management strategy. If we don’t have the necessary components to produce, nothing will function. But are all warehouse management strategies the same?
Certainly not, and over the years, different approaches have been developed.
Just in time
Just in Time management is a very lean approach, based on a warehouse that constantly reacts to the surrounding situation. In other words, raw materials are purchased only when there are orders.
This strategy is built on two essential pillars:
- Production materials must arrive when production begins.
- Production materials must not arrive before the start of production.
This may seem like a marginal detail, but when analyzed in the right context, it takes on a different relevance. Production cannot start without raw materials because the fundamental elements would be missing. On the other hand, having these elements too early in our warehouse could significantly increase management costs.
Just in case
The Just in Case model is a proactive model, the opposite of JiT, which is reactive. In this warehouse management approach, the aim is to predict demand and, consequently, production.
But what does predicting demand mean? It means constantly analyzing data flow and using cash flow to avoid blockage situations.
Indeed, demand peaks could create problems in the supply of raw materials, which would have serious consequences for our production.
Another factor to consider is supply chain issues. As the pandemic has taught us, the effects of an external shock can translate into gigantic supply problems.
We have seen the shortage of microchips leading to the slowdown in the tech sector and automotive industry, especially between 2021 and 2022.
When to use it?
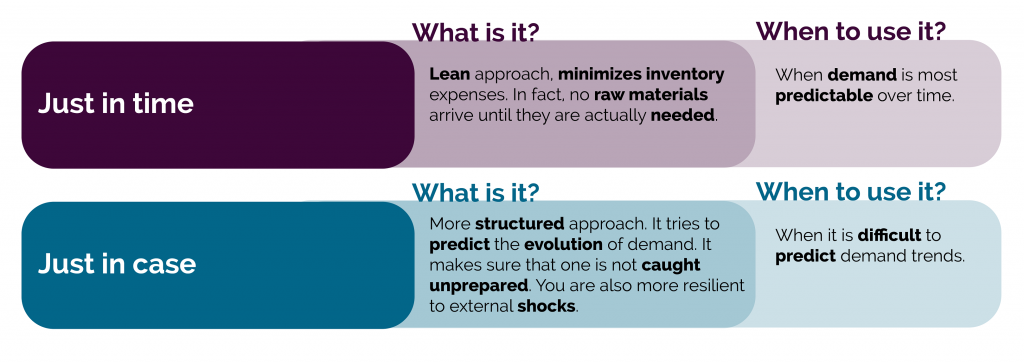
Is This Strategy Always Valid?
Over time, business needs can change significantly. Therefore, these two strategies should not be considered as something that never changes.
For example, JiT is certainly more suitable for smaller companies, which experience fewer demand shocks and have an easier time maintaining a valid supplier chain. Moreover, by reducing warehouse costs, they can invest in more critical areas for development.
On the other hand, the JiC strategy is more suitable for large companies with much longer supplier chains, which can cause more disruptions. Additionally, these companies generally have larger capital that they can still employ in other areas.
Leave A Comment