Origins
At the end of World War II, Japan found itself a defeated nation, paying a heavy toll in both lives and infrastructure. However, in this challenging climate, the need to resume production and work was paramount. Rebuilding not only the industries but also starting afresh from the basics was necessary to rebuild life after the war.
Interestingly, the origins of this methodology drew inspiration from one born in the USA. In the 1930s, engineer Walter Shewhart invented the “Plan-Do-Study-Act,” a simple yet effective approach to production.
The steps were as follows:
- Plan: Plan and understand how to address a problem.
- Do: Tackle the problem following your plan.
- Study: Analyze what you’ve done and identify areas for improvement.
- Act: Implement the plan if it worked; otherwise, restart the cycle.
A first evolution
The advantage of such an approach lies in increasing employees’ awareness and fostering a critical approach to problem-solving rather than a mechanical one.
Deming refined this concept by introducing “Total Quality Management,” emphasizing the need to understand both “special” and “common” causes of changes.
Special causes may be external to production, such as a natural disaster, while common causes consist of the everyday details that change, making identification challenging.
Initially, Deming’s approach did not gain traction in the USA, as the focus was on producing as much as possible to meet post-war consumption booms.
Arrival in Japan
Deming was sent, among others, to help revive Japan after its heavy defeat in World War II. Visionaries and intellectual leaders were needed to put the nation back on track.
Within a few decades, Japan’s GDP began to grow significantly, becoming the world’s second-largest economy in the 1970s. The country had successfully recovered. While the quality of the country’s manufacturing was already well-known, improvements were also attributed to figures like Deming, who received one of Japan’s highest honors.
Toyota: a striking example
Toyota applied this philosophy exceptionally well, competing in the automotive market even in the strong tradition of the American home market with prestigious brands.
Success resulted from:
- Reducing waste and activities deemed unproductive.
- Simplifying operations.
- Reducing production costs through the aforementioned points.
In the 1980s, vehicle production skyrocketed, and in 1986, Toyota became the first foreign brand in the USA to sell a million cars in a year, an extraordinary achievement for that era. This success was attributed to iconic models like the Toyota Corolla FX16.
Another pillar of Toyota’s automotive production was the Just-In-Time system: parts are delivered when needed, neither before nor after. This allowed cost containment and made the product much more competitive.
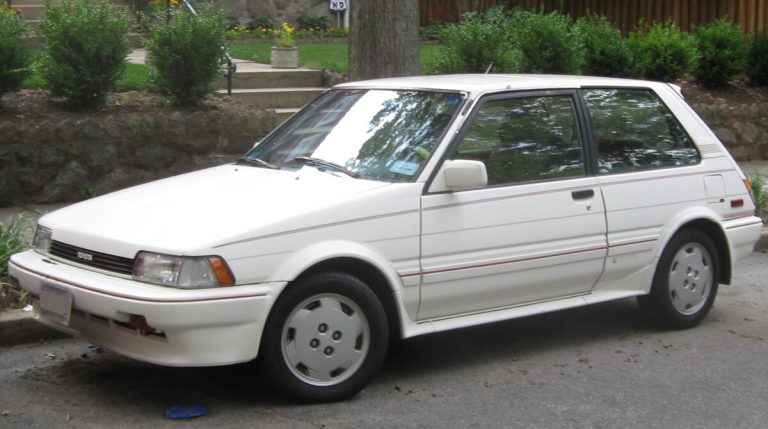
10 principles of Kaizen
1. Continuously improve
Strive for continuous improvement in all aspects of work and life.
2. Eliminate old concepts
Discard outdated ideas and approaches to make room for innovation.
3. No excuses, work hard
Avoid making excuses, and embrace hard work as the key to success.
4. Fearlessly implement new methods
Do not fear change; be bold in implementing new and improved methods.
5. Fix it if it’s broken
Address issues immediately; if something goes wrong, fix it promptly.
6. Empower everyone with problem-solving tools
Provide everyone with the tools and knowledge to contribute to problem-solving.
7. Seek input from multiple sources
Gather information and insights from various individuals to gain a comprehensive understanding.
8. Question before deciding
Before making decisions, ask why and strive to identify the root cause.
9. Save on small things to invest in the future
Practice frugality on minor expenses to invest in future improvements.
10. Never stop improving
Maintain a relentless commitment to continuous improvement.
Gemba and Kaizen
The term “Gemba” translates to the “real place,” indicating the actual workplace, such as a factory. This implies that Kaizen must be grounded in reality. Solutions are ineffective if they are devised without experiencing the environment where the actual work takes place.
Practices for Gemba and Kaizen
Address issues immediately:
- When a problem arises, go directly to Gemba.
- Inspect machines and tools, ensuring everything is in order.
- Take immediate countermeasures.
Identify the root cause:
- Find the cause of the problem.
- Standardize the solution to prevent problem recurrence.
One Reply to “Kaizen: a curious story”
[…] seen in a previous article dedicated to Kaizen, structured approaches enable better progress and a thorough analysis of what happens within a […]