Le origini del Kaizen
Alla fine della Seconda Guerra Mondiale, il Giappone si trovava in una situazione critica: infrastrutture devastate, economia in ginocchio e una necessità impellente di ripartire. Fu in questo contesto che emerse il Kaizen, un metodo di miglioramento continuo ispirato a principi già esistenti negli USA.
Negli anni Trenta, l’ingegnere americano Walter Shewhart sviluppò il ciclo Plan-Do-Study-Act (PDSA):
- Plan: pianificare la soluzione di un problema;
- Do: implementare il piano;
- Study: analizzare i risultati e identificare margini di miglioramento;
- Act: standardizzare il miglioramento o ripetere il ciclo.
Il concetto venne poi perfezionato da W. Edwards Deming, che introdusse il Total Quality Management (TQM), distinguendo tra cause “speciali” (eventi eccezionali) e “comuni” (piccoli cambiamenti quotidiani nella produzione). Tuttavia, negli USA, il metodo inizialmente non riscosse successo, poiché le industrie erano concentrate sulla produzione di massa.
L’arrivo del Kaizen in Giappone
Negli anni ’50, Deming fu invitato in Giappone per contribuire alla rinascita industriale. Qui il suo metodo trovò terreno fertile, portando il paese a una crescita economica straordinaria. Già negli anni Settanta, il Giappone divenne la seconda potenza economica mondiale.
Uno dei settori che adottò più efficacemente il Kaizen fu l’automotive, con un protagonista indiscusso: Toyota.
Toyota e l’evoluzione del Kaizen
Toyota trasformò il concetto di Kaizen in un sistema produttivo rivoluzionario:
- Riduzione degli sprechi e delle attività non produttive.
- Semplificazione dei processi per aumentarne l’efficienza.
- Ottimizzazione dei costi attraverso l’eliminazione degli eccessi.
Uno dei pilastri di questa filosofia è il Just In Time (JIT): ogni componente viene prodotto e consegnato solo quando necessario, riducendo gli stock e ottimizzando il flusso produttivo. Questo sistema portò Toyota a risultati straordinari, come il superamento della soglia di 1 milione di auto vendute negli USA nel 1986, grazie a modelli iconici come la Toyota Corolla FX16.
I 10 principi del Kaizen
Il Kaizen non è solo una metodologia industriale, ma un vero e proprio approccio al miglioramento continuo. Ecco i suoi 10 principi fondamentali:
- Migliora continuamente.
- Elimina i concetti obsoleti.
- Non darti scuse, lavora sodo.
- Non temere il cambiamento.
- Se qualcosa va storto, correggilo subito.
- Fornisci gli strumenti giusti a tutti.
- Raccogli informazioni da più fonti.
- Prima di decidere, chiediti perché? per arrivare alla radice del problema.
- Risparmia su piccole cose per investire nel futuro.
- Non smettere mai di migliorare.
Gemba e Kaizen: il miglioramento alla fonte
Nel Kaizen si applica il concetto di Gemba, che in giapponese significa “posto reale“. Il miglioramento deve avvenire sul campo, dove si svolgono le operazioni concrete. Per questo, in caso di problemi, si seguono queste regole:
- Recarsi immediatamente sul posto.
- Controllare macchinari, strumenti e processi.
- Prendere contromisure immediate.
- Individuare la causa del problema.
- Standardizzare la soluzione per prevenire ricorrenze.
Kaizen e Lean Production
Il Kaizen si inserisce perfettamente nel modello della Lean Production, che mira a minimizzare gli sprechi e massimizzare il valore. Alcuni strumenti chiave della lean organization includono:
- 5S: Seiri (Ordine), Seiton (Stabilizzazione), Seiso (Pulizia), Seiketsu (Standardizzazione), Shitsuke (Disciplina).
- Just in Time: riduzione degli stock e produzione a flusso continuo.
- Kanban: sistema di gestione visiva del lavoro.
- Poka-Yoke: prevenzione degli errori mediante soluzioni semplici.
- Andon e OEE: monitoraggio e miglioramento della produttività.
Kaizen: un metodo applicabile ovunque
Oggi il Kaizen non è solo un metodo per le aziende manifatturiere. La sua filosofia viene adottata in svariati settori, dalla sanità alla tecnologia, dal marketing alla crescita personale.
Grazie al suo approccio graduale e sistematico, il Kaizen si conferma uno strumento potente per migliorare qualsiasi processo, riducendo sprechi e aumentando l’efficienza in ogni ambito.
Conclusione
Se ti stai chiedendo “Kaizen cos’è?”, la risposta è chiara: è un metodo di miglioramento continuo nato in Giappone, reso celebre da Toyota e oggi utilizzato in tutto il mondo. Basato su piccoli passi, analisi costante e coinvolgimento di tutti, il Kaizen permette di ottimizzare ogni processo, portando aziende e persone verso l’eccellenza.
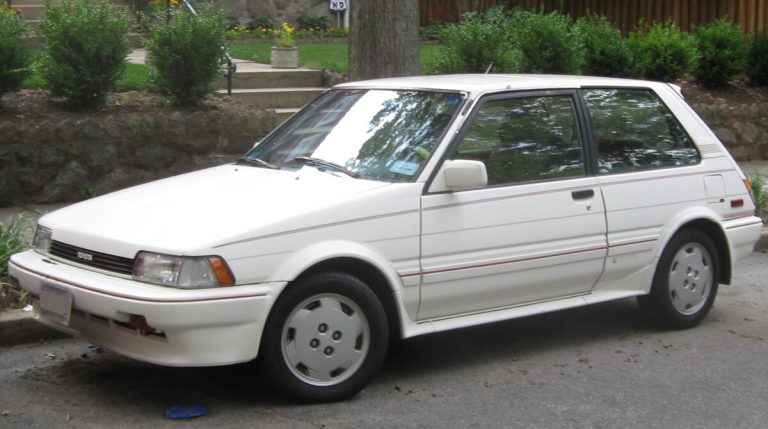
Leave A Comment